Our indoor air is polluted, but new materials could provide solutions
Frédéric Thévenet, IMT Lille Douai – Institut Mines-Télécom
We spend 80% of our lives in enclosed spaces, whether at home, at work or in transit. We are therefore very exposed to this air, which is often more polluted than outdoor air. The issue of health in indoor environments is thus associated with chronic exposure to pollutants and to volatile organic compounds (VOCs) in particular. These species can cause respiratory tract irritation or headaches, a set of symptoms that is referred to as “sick building syndrome.” One VOC has received special attention: formaldehyde. This compound is a gas at room temperature and pressure and is very frequently present in our indoor environments although it is classified as a category 1B CMR compound (carcinogenic, mutagenic, reprotoxic). It is therefore subject to indoor air quality guidelines which were updated and made more restrictive in 2018.
The sources of volatile organic compounds
VOCs may be emitted in indoor areas by direct, or primary sources. Materials are often identified as major sources, whether associated with the building (building materials, pressed wood, wood flooring, ceiling tiles), furniture (furniture made from particle board, foams), or decoration (paint, floor and wall coverings). The adhesives, resins and binders contained in these materials are clearly identified and well-documented sources.
To address this issue, mandatory labeling has existed for these products since 2012: they are classified in terms of emissions. While these primary sources related to the building and furniture are now well-documented, those related to household activities and consumer product choices are more difficult to characterize (cleaning activities, cooking, smoking etc.) For example, what products are used for cleaning, are air fresheners or interior fragrances used, are dwellings ventilated regularly? Research is being conducted in our laboratory to better characterize how these products contribute to indoor pollution. We have recently worked on cleaning product emissions and their elimination. And studies have also recently been carried out on the impact of essential oils at our laboratory (at IMT Lille Douai) in partnership with the CSTB (French National Scientific and Technical Center for Building) in coordination with ADEME (French Environmental and Energy Management Agency).
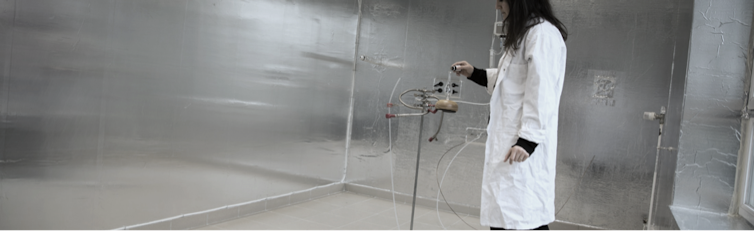
Emission, deposition and reactivity of essential oils in indoor air (Shadia Angulo-Milhem, IMT Lille Douai). Author provided
In addition to the primary sources of VOCs, there are also secondary sources resulting from the transformation of primary VOCs. These transformations are usually related to oxidative processes. Through these reactions, other kinds of VOCs are also formed, including formaldehyde, among others.
What solutions are there for VOCs in indoor air?
Twenty years ago, an approach referred to as a “destructive process” was being considered. The idea was to pass the air to be treated through a purification system to destroy the VOCs. These can either be stand-alone devices and therefore placed directly inside a room to purify the air, or integrated within a central air handling unit to treat incoming fresh air or re-circulated air.
Photocatalysis was also widely studied to treat VOCs in indoor air, as well as cold plasma. Both of these processes target the oxidation of VOCs, ideally their transformation into CO2 and H2O. Photocatalysis is a process that draws on a material’s – usually titanium dioxide (TiO2) – ability to adsorb and oxidize VOCs under ultraviolet irradiation. Cold plasma is a process where, under the effect of a high electric field, electrons ionize a fraction of the air circulating in the system, and form oxidizing species.
The technical limitations of these systems lie in the fact that the air to be treated must be directed and moved through the system, and most importantly, the treatment systems must be supplied with power. Moreover, depending on the device’s design and the nature of the effluent to be treated (nature of the VOC, concentration, moisture content etc.) it has been found that some devices may lead to the formation of by-products including formaldehyde, among others. Standards are currently available to oversee the assessment of this type of system’s performance and they are upgraded with technological advances.
Over the past ten years, indoor air remediation solutions have been developed focusing on the adsorption – meaning the trapping – of VOCs. The idea is to integrate materials with adsorbent properties in indoor environments to trap the VOCs. We have seen the emergence of materials, paint, tiles and textiles that incorporate adsorbents in their compositions and claim these properties.
Among these adsorbent materials, there are two types of approaches. Some trap the VOCs, and do not re-emit them – it’s a permanent, irreversible process. The “VOC” trap can therefore completely fill up after some time and become inoperative, since it is saturated. Today, it seems wiser to develop materials with “reversible” trapping properties: when there is a peak in pollution, the material adsorbs the pollutant, and when the pollution decreases, for example, when a room is ventilated, it releases it, and the pollutant is evacuated through ventilation.
These materials are currently being developed by various academic and industry players working in this field. It is interesting to note that these materials were considered sources of pollution 20 years ago, but can now be viewed as sinks for pollution.
How to test these materials’ ability to remove pollutants
Many technical and scientific obstacles remain, regardless of the remediation strategy chosen. The biggest one is determining whether these new materials can be tested on a 1:1 scale, as they will be used by the end consumer, meaning in “real life.”
That means these materials must be able to be tested in a life-size room, and with conditions that are representative of real indoor atmospheres, while controlling environmental parameters perfectly. This technical aspect is one of the major research challenges in IAQ since it determines the representativeness and therefore the validity of the results we obtain.
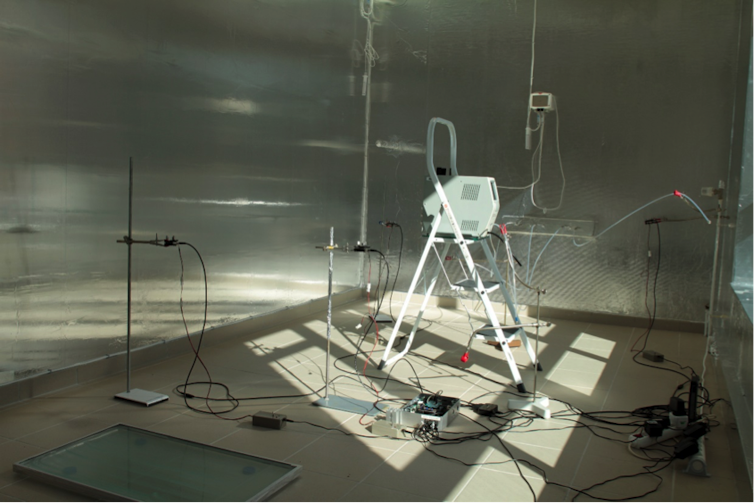
Experimental IRINA room (Innovative Room for Indoor Air studies, IMT Lille Douai). Author provided
We developed a large enclosed area in our laboratory for precisely this purpose a few years ago. With its 40 square meters, it is a real room that we can go into, called IRINA (Innovative Room For Indoor Air Studies). Seven years ago, it was France’s first fully controlled and instrumented experimental room on a 1:1 scale. Since its development and validation, it has housed many research projects and we upgrade it and make technical updates every year. It allows us to recreate the indoor air composition of a wood frame house, a Parisian apartment located above a ring road, an operating room and even a medium-haul aircraft cabin. The room makes it possible to effectively study indoor air quality and treatment devices in real-life conditions.
Connected to this room, we have a multitude of measuring instruments, for example to measure VOCs in general, or to monitor the concentration of one in particular, such as formaldehyde.
Frédéric Thévenet, Professor (heterogeneous/atmospheric/indoor air quality physical chemistry), IMT Lille Douai – Institut Mines-Télécom
This article has been republished from The Conversation under a Creative Commons license. Read the original article (in French).