Taking 3D printing to the next level
At the beginning of 2018, IMT Lille Douai unveiled an additive manufacturing platform dedicated to manufacturing large-scale parts: LASCALA. This equipment is a worldwide innovation. Its capacity to use any type of polymer even enables it to print 3D composite parts measuring several meters. The scientific challenge has been successfully met and has opened up a whole new realm of possibilities for manufacturers.
Do you think you know what a 3D printer is like? With LASCALA*, the additive manufacturing platform, you are in for a surprise. Forget a printhead measuring a few square centimeters sliding along a rod the length of a school ruler. With its 6-axis industrial robot spanning over 2 m and a maximum load capacity of 150 kg, LASCALA is no desktop 3D printer. Located in the facilities of IMT Lille Douai, the printer is destined to take polymer-based additive manufacturing to the next level of its industrial potential. Up until now this design technique was only available for small-scale plastic parts of a few cubic centimeters. With LASCALA, the 3D-printed parts could reach dimensions of several meters and be fiber-reinforced.
The platform has been functional since January 2018 and is a major innovation in the sector. Using a 6-axis robot alone significantly distinguishes LASCALA from the solutions implemented on other additive manufacturing systems. The logical choice would have been to use a traditional construction with a gantry and printhead moving along it. In other words, reproducing a larger scale of what already exists. Yet the robotic arm introduces the advantage of 7 degrees of freedom: 6 axes of rotation and 1 plane of movement. The printhead attached to its end can therefore rotate in every direction and move in every direction in space.
https://www.youtube.com/watch?v=7WH9iQg3yFU
Another convincing argument: long-term, this system is more technologically advantageous. “Usually a 3D printer superimposes planar layers,” explains Jérémie Soulestin, a researcher in materials science at IMT Lille Douai in charge of LASCALA. This causes a staircase effect on the edges of the parts: when a smaller layer is added to another, they form a step. “With the robot, we will be able to develop curved layers, which will limit this effect,” he continues. This new construction method using curved layers has a positive effect on the aesthetic aspect as well as on the parts’ mechanical properties.
The move towards 3D printing for composites
While LASCALA is the first platform of its kind, the team at IMT Lille Douai is not the only one to have attempted large-scale 3D printing. Local Motors, for example, was the first company to offer a car—named Strati— made of polymer materials entirely produced using 3D printing. Yet none of the attempts to date have developed machines flexible enough to deposit any type of polymer material in any direction. Most of the time, the manufacturer of the 3D printer even limits the materials that are compatible with the 3D-printing process. LASCALA, on the other hand, offers free-form design in terms of the choice of plastic materials. “This argument and the idea of not being limited by this constraint are what convinced us to develop our own machine,” Jérémie Soulestin explains.
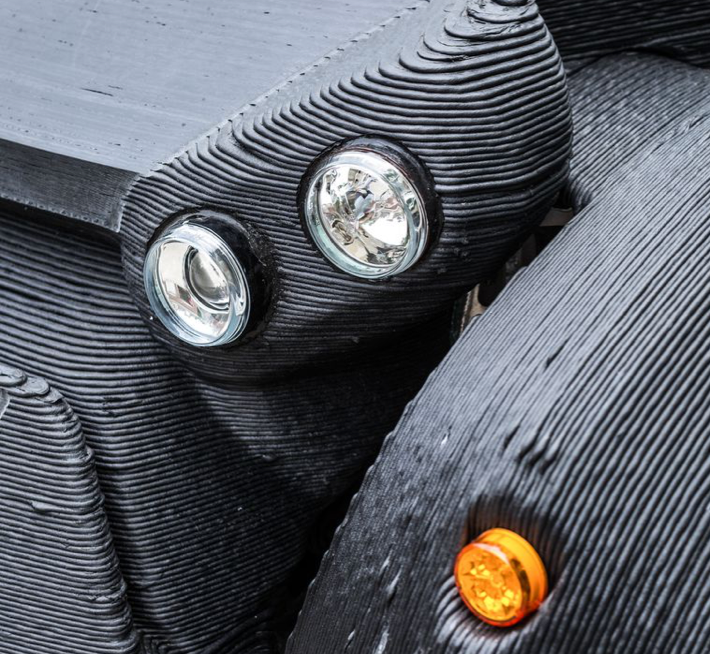
The Strati by Local Motors, a roadster prototype produced using large-scale 3D printing. Its appearance highlights one of the problems to solve in additive manufacturing at this scale: the staircase effect.
And because they were now the masters of the machine they designed, the researchers were able to take their original idea a step further. The printhead contains an extrusion device: “an endless screw in a heated barrel pushes the material through a nozzle that deposits a melted filament,” the researcher explains. The shape of the nozzle can be adapted to deposit the filament in different ways and enables to improve the part quality. In addition, two materials can be deposited within the same melted filament, thus creating a material with a polymer core and an outer skin made of another plastic.
Finally, the researchers insisted on designing a platform that would be adapted to the industrial uses of the future. The printhead is therefore capable of depositing fiber-reinforced polymers. LASCALA can therefore use 3D-printing to produce composite materials with short, chopped fibers and even with continuous fibers. This special feature makes the platform worthy of being presented at the largest annual global meeting in the field of composites: the JEC World show, which will be held from March 6-8 in Paris. The equipment’s capabilities cannot help but attract manufacturers. “We knew that the aeronautics sector would be interested, but we were surprised the automotive sector contacted us so quickly,” says Jeremie Soulestin. LASCALA will still need nearly a year to transition from “functional” to fully “operational”. One year of optimization before this technical innovation begins producing impressive projects that will prepare the manufacturing processes of the future.
*LASCALA, LArge SCALe plAstics & composites 3D printing, receives support from the Hauts-de-France Region and is co-funded by the European Union
Also read on I’MTech: