Eikosim improves the dialogue between prototyping and simulation
Simulate. Prototype. Measure. Repeat. Developing an industrial part inevitably involves these steps. First comes the digital model. Then, its characteristics are assessed through simulation, after which, the first version of the part is built. The part must then be subject to mechanical stress to assess its resistance and be closely observed from every angle. The test results will be used to improve the modelling, which will produce a new prototype… and so the cycle continues until a satisfactory version is produced. But Renaud Gras and Florent Mathieu want to reduce the repetitions involved in this cycle, which is why they created Eikosim, a startup that has been incubating at Paristech Entrepreneurs for one year. They develop software specialized in helping engineers with these design stages.
So, what is the key to saving as much time as possible? Facilitating the comparison between the digital tests and the measurements. Eikosim meets this need by integrating the measurement results recorded during testing directly into the part’s digital model. Any deformation, cracking or change in the mechanical properties is therefore recorded in the digital version of the object. The engineers can then easily compare the changes measured during the tests with those predicted during simulation, and therefore automatically correct the simulation so that it better reflects reality. What this startup offers is a breakthrough solution, since the traditional alternative involves storing the real measurements in a data table, and creating algorithms for manually readjusting the part through simulation. A tedious and time-consuming process.
Another strength the startup has to offer: its software can optimize the measurements of prototypes, for example by facilitating the positioning of observation cameras. One of the challenges is to ensure their actual position is well calibrated to correctly record the movements. To achieve this, the cameras are usually positioned using an alignment jig and arranged using a complex procedure which, again, is time-consuming. But the Eikosim software makes it possible to directly record the cameras’ positions on a digital model of the part. Since an alignment jig is no longer needed, the calibration is much faster. The technology is therefore compatible with large-scale parts, such as the chassis of trains. These dimensions are too large for technology offered by competitors, which struggles to arrange many cameras around such enormous parts.
The startup’s solutions have won over manufacturers, especially in aeronautics. The sector innovates materials, but must constantly address safety constraints. The accuracy of the simulations is therefore essential. In this industry, 20% of engineers’ time is spent making comparisons between simulation and real tests. The powerful software developed by Eikosim is therefore represents an enormous advantage in reducing development times.
The founders
[divider style=”normal” top=”20″ bottom=”20″]
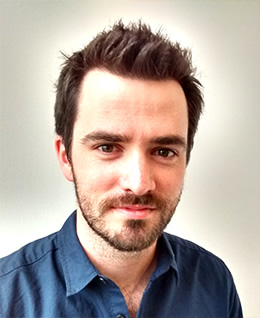
Florent Mathieu
Renaud Gras and Florent Mathieu founded Eikosim after completing a thesis at the ENS Paris-Saclay Laboratory of Mechanics and Technology. Equipped with their expertise in understanding the mechanical behavior of materials by instrumenting tests using imaging techniques, they now want to use their startup to pass these skills on to the manufacturing industry.
[divider style=”normal” top=”20″ bottom=”20″]
Leave a Reply
Want to join the discussion?Feel free to contribute!