Composite Materials: the race to keep going faster
In the world of materials, composites are currently undergoing a transformation that is just a significant as the plastics boom in the 1960s. To massively integrate these materials into high-volume production markets—automotive, aeronautics, rail, etc.—manufacturers must further reduce the time it takes to mold the parts. This complex goal is attainable by redesigning the materials’ composition and architecture, adapting the manufacturing processes used, and relying on new digital simulation tools.
“Fifteen years ago, we were happy when we could produce a complex part made of structural composites in five minutes,” recalls Patricia Krawczak, a materials researcher at IMT Lille Douai. In 2017, the requirements are more demanding. Many sectors are interested in the mechanical properties that composites have to offer, including the transportation industry. These new materials—which are more resistant, lighter, and more durable—pave the way for breakthrough products, and offer new economic opportunities. It is therefore necessary to be able to integrate them massively into markets with high-production volumes, such as the automotive industry. According to the Industry of the Future Alliance, the greatest industrial challenges currently facing composite materials are the reduction of molding cycle and manufacturing times, and the development of “high-speed” processes. For automotive parts, the target is set at around one minute.
Also read on I’MTech What is a composite material?
At the request of manufacturers, scientists are working to meet this challenge. To do so, the plastic resins used as the matrices to impregnate fiber reinforcements have already been modified for some time now. Researchers have switched from thermosetting resins—which harden when heated—to thermoplastic resins, which melt with heat and harden as the part returns to room temperature. “Cure times for thermosetting resins are fairly long, even though the suppliers of these matrices are making progress and working to reduce them,” explains Patricia Krawczak. However, thermoplastic resins can be shaped quickly, for example by using a hot-pressing process, stamping, or using injection technology on a fiber preform, without the need for any further curing. “In this respect, these resins can help reduce the cycle time,” the researcher explains.
A comprehensive “materials/process/products” approach
However, modifying the nature of the resin isn’t all that is required to reduce manufacturing time. In order for parts to feature high mechanical performance properties, defects, such as air bubbles trapped in the material, must be avoided at all costs. It is therefore necessary to ensure that the thermoplastic resin completely penetrates between the reinforcement fibers once it has become liquid through increased temperature. Yet these resins are known for being more viscous than thermosetting resins. Scientists must reduce the viscosity of these resins to gain a competitive edge and take advantage of the thermoplastics’ capacity to be shaped quickly. “We are working with chemists to develop polymers that retain the same properties once they become solid, while being more fluid at the processing temperature,” Patricia Krawczak explains.
Researchers in materials science can also adapt the architecture of the reinforcements. Within composite materials are fibers that form strands composed of filaments. They can be assembled–woven, braided or sewn–in different ways. “The way the reinforcement is formed affects the properties of the final composite material, as well as the permeability of the fiber preform, which therefore influences how the resin flows into the reinforcement,” Patricia Krawczak notes. In order to find the best structure, with the right balance between mechanical properties and sufficient permeability, the researcher’s team is also working with fiber reinforcement designers.
Another available means of action lies in the manufacturing process itself, particularly by adapting it to the specific characteristics of the materials that make up the composite itself: the polymer matrix and the reinforcement fiber. “Our team has developed fast hybrid processes that integrate several steps into a single molding operation, for example by combining resin transfer molding and compression molding, or thermoforming/stamping of local composite inserts and overmolding,” Patricia Krawczak explains. In addition to the shortened manufacturing cycle, this mix of processes significantly reduces the number of basic components that must be assembled to produce a complex part. This is a significant benefit for the plastic parts manufacturers that partner with IMT Lille Douai.
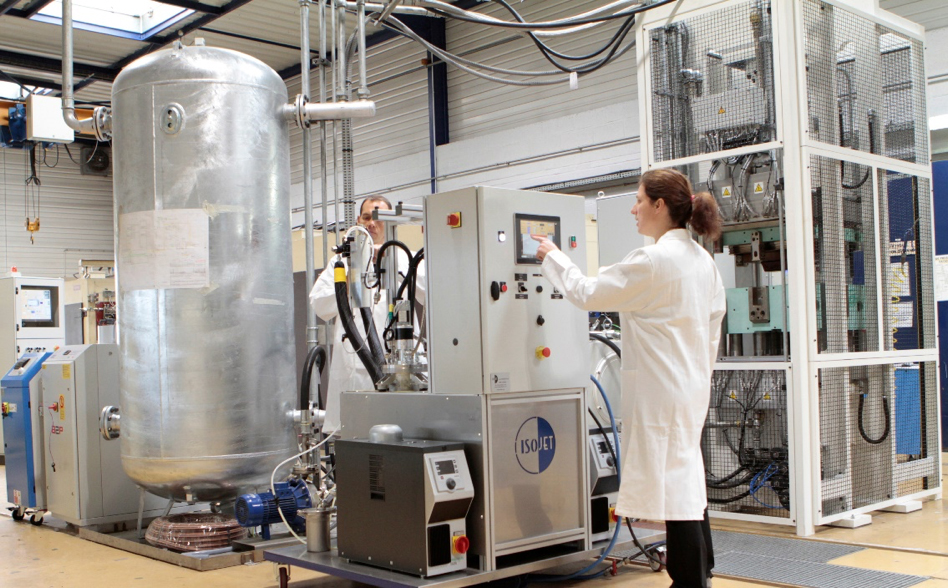
Optimization platform for new composite processes (POPCOM). Photo: IMT Lille Douai.
Digital technology helps identify optimal materials-process pairings
In practice, composite materials offer a very impressive range of “matrix polymer / fiber reinforcement / manufacturing process” combinations, which has been further increased by recent innovations from producers—chemists and textile manufacturers—and processors. To speed up the design of industrial parts, researchers develop virtual engineering chains. Using a technological platform equipped with prototype tools and demonstrators that represent industrial manufacturing processes, they analyze, identify and model impregnation mechanisms. They therefore complement and improve on the manufacturing numerical simulation tools.
“For example, a few years ago we worked with a highly reactive resin that had a gel time of one minute,” says Patricia Krawczak. “But at the time, the available simulation software did not take into account the spatial and temporal variations in the viscosity of these very fast-polymerizing resins. We therefore had to update the digital tool by incorporating a specific model combining thermokinetic reactions and flow”. It was then possible to properly simulate the impregnation of different types of reinforcements with this resin on geometrically complex automotive body parts. By conducting numerical tests, many more combinations have been explored. Researchers can work faster and identify the best configurations to optimize manufacturing technologies. They can therefore successfully reduce cycle times while still maintaining the level of quality and performance.
By studying the materials virtually, as well as the processes used, scientists can dare to explore methods that seem counter-intuitive. This was the case during a European project in which IMT Lille Douai partnered with manufacturers to reduce the molding cycle time for the floor structure of a motor vehicle. “By having our models integrate the way fiber fabrics are distorted during the draping procedure and the consequences this has on the local flow of resin, we were able to simulate a process. We proposed inlet points for the sequential injection of resin, distribution channels and vents at areas on the part that were not the most logical choices for manufacturers,” Patricia Krawczak recalls. But the numerical model had accurately predicted that the resin would impregnate the reinforcement faster and in a more homogeneous manner using this strategy. This result was then confirmed through full-scale experimental validations.
Today, the researchers continue to pursue this scientific approach—supported by industrial collaborations—to explore the potential of new materials and innovative processes. The digital tools are adapted to accurately simulate new technological alternatives and respond to the growing demand for natural fibers in composite materials. Due to their porous nature, they absorb part of the resin and swell. This phenomenon must therefore be included in the simulations, in hopes that this will lead to the discovery of new, more efficient scenarios. Cycle times are no longer improved by several minutes, like they were fifteen years ago; now they are improved by tens of seconds. This gain is still a considerable one in industries that can potentially produce thousands of composite parts each day.
Find out more about natural fiber-based high-performance composites:
Leave a Reply
Want to join the discussion?Feel free to contribute!