What is a composite material?
Mines Saint-Étienne, answers our questions in this new addition to the “What is…?” series, dedicated to composite materials.
Composite materials continue to entice researchers and are increasingly being used in transport structures and buildings. Their qualities are stunning, and they are considered to be indispensable in addressing the environmental challenges at hand: reducing greenhouse gas emissions, creating stronger and more durable building structures, etc. How are these materials designed? What makes them so promising? Sylvain Drapier, a researcher in this field at
Does the principle behind a composite mean that it consists of two different materials?
Sylvain Drapier: Let’s say at least two materials. For a better understanding, it’s easier to think in terms of volume fractions, in other words, the proportion of volume that each component takes up in the composite. In general, a composite contains between 40 to 60% of reinforcements, often in the form of fibers. The rest is made up of a binder, called the matrix, which allows for the incorporation of these fibers. Increasingly, the binder percentage is being reduced by a few percentage points in order to add what we call fillers, such as minerals, which will optimize the composite material’s final properties.
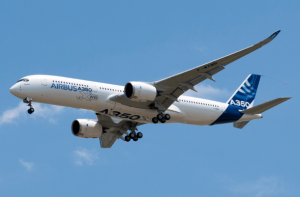
50 % of the structure of the Airbus A350 is made of composite materials. The transportation industry is particularly interested in these materials.
Are these fibers exactly like those in our clothing?
SD: Agro-sourced composites, using natural fibers like flax and hemp, are starting to be developed. In this regard, it’s a little like the fibers in our clothing. But these materials are still rare. For composites that are produced for widespread distribution, the fibers are short — at times extremely short — glass fibers. To give an idea of their size, they have a diameter of 10 micrometers and are 1 to 2 millimeters long. They can be larger in products that must absorb limited strain, such as sailboards and electrical boxes, in which they are a few centimeters long. However, high-performance materials require continuous fibers that measure up to several hundred meters, which are wound on reels. This is the case for aramid fibers, with the best known being Kevlar, and is the case for glass fibers used to make wind turbine blades, as well as for carbon fibers used in structures that must withstand heavy use, such as bicycles, high-end cars and airplanes …
Can these fibers be bound together by soaking them in glue to form a composite?
SD: It all starts with fiber networks, in 2D or 3D, produced by specialized companies. This involves textiles that are actually woven, or knitted, in the case of revolving parts. After this, there are several production methods. Some processes involve having the plastic resin, in liquid form, soak into this network as a binder. When heated, the resin hardens: we refer to this as a thermosetting polymer. Other polymer resins are used in a solid state, and melt when heated. They fill the spaces between the fibers, and become solid when they return to room temperature. These matrices are called thermoplastic, made from the same polymer family as the plastic recyclable products we use every day. Metal and ceramic matrices exist too, but they are rarer.
How is the choice of fiber determined?
SD: It all depends on its use. Ceramic matrices are used for composites inserted into hot structures; thermoplastic resins melt above 200-350°C, and the thermosetting matrices are weakened above 200°C. Some uses require very unusual matrix choices. This is the case for Formula 1 brakes, and the Ariane rocket nozzles, designed with 3D carbon: not only are the fibers carbon, but the binder is carbon too. Compared with a part made completely of carbon, this composite resists much better to crumbling, and can used at temperatures well in excess of 1,000°C.
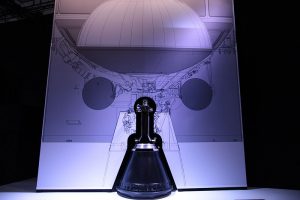
The Vinci motor is made for European space agency rockets. Its nozzle (the black cone in the picture), which enables the propulsion, is made of a carbon-carbon composite. Credits: DLR German Aerospace Center.
What are the benefits of composites?
SD: These materials are very light, while offering physical properties that are at least equivalent to those of metallic materials. This benefit is what has won over the transportation industry, since a lighter vehicle consumes less energy. Another benefit of composites is they do not rust. Another feature: we can integrate functions into these materials. For example, we can make a composite more flexible in certain areas by orienting the fibers differently, which can allow sub-assemblies of parts to be replaced by just one part. However, composite resins are often water-sensitive. This is why the aeronautics industry simulates ageing cycles in specific humidity and temperature conditions.
What approach is envisaged for recycling composites?
SD: Thermoplastic matrices can be melted. The polymers are then separated from the fibers and each component is processed separately. However, thermosetting matrices lack this advantage, and the composites they form must be recycled in other ways. It is for this reason that researchers, seeking materials with a reduced carbon footprint, are looking to agro-based composites, by using more and more plant fibers. There are even composites that are 100% agro-based, associating bio-sourced polymers with these organic reinforcements. Composite recycling concerns do not yet attract the attention they deserve, but research teams are currently investing in this means of development.
Read more on our blog
Leave a Reply
Want to join the discussion?Feel free to contribute!