Agro-based composite materials – a Mines area of expertise
The materials of the future need to be more than just high-performance. They must also be environmentally friendly: more recyclable and based on renewable resources. This is why scientists and industrialists are taking a closer look at composite materials developed from plant fibers. They represent a major research focus for Institut Mines-Télécom (IMT) schools — especially at Mines Alès and Mines Douai — which participated in the symposium on March 30th on “Materials: realities and new frontiers”.
Patricia Krawczak is convinced: for certain structures, composite materials developed from plant fibers can now compete with those developed with fiberglass. This researcher from Mines Douai, who led the session on “The opportunities and limits of eco-materials” at the IMT Materials symposium at the end of March, has been working on this topic for around ten years. She has witnessed the emergence and development of these agro-based composites: “In the beginning, it was just plastics reinforced with short lengths of natural fibers (flax, hemp, or cellulose and wood). This produced materials with poor mechanical performance,” she explains. It is only over the past few years that the industrial field has been restructured to develop solutions capable of manufacturing high-performance parts with a rigidity, strength and durability comparable to fiberglass, which currently predominates. “Agro-based composites are no longer used only as cladding components; they can also be used to develop semi-structural parts,” explains Patricia Krawczak. This is the case in transport sectors (automobile, aeronautics, rail, ship building, etc.) and in the building sector.
Among the plants tested for these new uses, flax and hemp stand out from the others, especially in France. They have the advantage of being abundant resources in our country. As Patricia Krawczak reminds us, “the emergence of agro-based materials is rooted in a sustainable development approach.” The use of plant fibers can potentially result in composites that are more easily recycled. The use of local crops therefore enables supply and transport with a low carbon footprint, consistent with this principle of limiting the impact on the environment. In addition to being abundant, these plants also offer benefits of a scientific and technical nature. A great deal of work is being carried out to improve the understanding and mastery of the resulting composite materials.
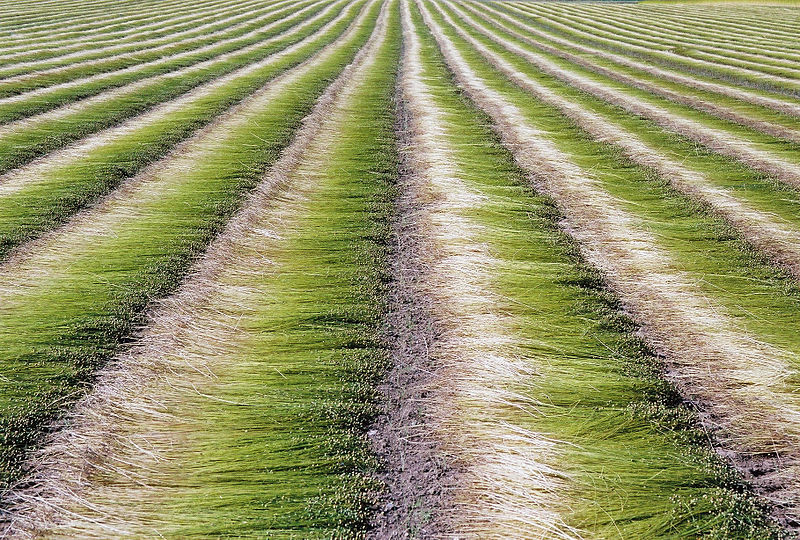
France is the world’s leading producer of textile flax. Credits: BERTFR.
Mastering the performance of agro-based composites
At Mines Alès, Anne Bergeret’s team is therefore seeking to identify the parameters that influence the wear properties of plant fiber-based composites, such as mechanical properties, thermal stability, and durability. The manner in which the plant fibers are dispersed within the polymer matrix has proven to be a key parameter. This depends on the fiber’s intrinsic characteristics, such as its chemical composition, surface chemistry, structure, and the application conditions. Another decisive parameter is the quality of the interface between the plant fiber and the polymer matrix. Research carried out at Mines Alès has shown that certain plant fiber treatments, though commonly used, such as caustic soda processing, have an impact on the fiber’s structure, and therefore on its properties and state of dispersion within the matrix. In light of this paradox, Anne Bergeret reminds us of “the need for a full understanding of the fiber’s processing conditions and the application of agro-based composites”.
“If a part needs to conform to a particular functional specification or a specific request, lightening the material at the expense of its strength and rigidity is not a solution”
This a view shared by Patricia Krawczak, whose research work at Mines Douai has also been subject to a compromise between lightening and performance. “If a part needs to conform to a particular functional specification or a specific request, lightening the material at the expense of its strength and rigidity is not a solution. Therefore, we always think in terms of specific properties, in other words, performance/density ratios,” she explains. This partially explains why plant fibers can compete with fiberglass for certain uses, but will probably not rival carbon fiber, which has an indisputably superior mechanical property/density ratio.
Integrating the specific characteristics of natural fibers into digital simulation tools
Despite the performance characteristics of plant fibers, such as flax, they are in no position to replace more conventional fibers in all product specifications. To think otherwise would be to ignore the intrinsic characteristics of these fibers. Plants, by their nature, have variable characteristics, due to their growing conditions (seasonality, climate, place of production, etc.). They are also porous, which makes their fibers sensitive to humidity. They also have a low level of tolerance for high temperatures; it would therefore be difficult to associate them with polymer matrices with forming processes that require heating to very high temperatures. But agro-based composites are already highly suitable for use in more favorable conditions, in which their sensitivity to humidity does not present a problem, or by associating them with polymer matrices that can be transformed at lower temperatures. Furthermore, research is underway to remedy these problematic aspects. The goal is to make natural fiber reinforcements water-repellent, or to adapt plastic manufacturing processes to allow for the production of composite parts under gentler conditions.
“We will not be able to compensate for the porous nature of the fibers, and it will be difficult to overcome their variable characteristics due to their natural origin,” Patricia Krawczak points out. “However, we can make sure these specific features are taken into account in the models and simulations, and in this way ensure that designers, processers and users of industrial parts fully understand the behavior of agro-based composites.” The development of the virtual engineering chain for these materials is booming. The same is true for the market growth of these agro-based composites. “Industrialists from different fields of application are open to using them, but will only do so if the simulation tools they use in their design offices are compatible,” explains the researcher. Her team is working on these aspects as well.
Turning the weaknesses of the plant fibers into strengths
While in Mines Douai scientists are focusing on modeling in order to better understand the limits of plant fibers, Anne Bergeret and her team at Mines Alès are seeking to turn these limitations into advantages. The plants have low thermal stability (decomposition beginning at 250°C), making them relatively inflammable. However, they have the particular feature of forming a stable carbonaceous residue after decomposition. The combustion of flax-based composites therefore produces this residue on the surface, which has the property of protecting the underlying material and slowing down its deterioration. Anne Bergeret’s team has therefore sought to promote this appearance of charred residue by grafting phosphorous flame-retardants onto the surface of fibers. The results have shown an improvement in the reaction to fire, and should therefore improve the resilience of the composite, whose structure will be less severely damaged.
Whether the aim is to understand the limitations of agro-based composites or to take advantage of them, either way, researchers are dedicated to using biomass and turning it into new useful materials for the industrial sectors seeking innovations — in aeronautics, as well as in electronics and medical equipment. With them, the sectors are being reorganized, through projects like Fiabilin (PIA-PSPC) and Sinfoni (PIA-PSPC), in which Mines Douai has participated, and Enafilia (ADEME) and Hermes (H2020), with the involvement of Mines Alès, involving flax and hemp growers alongside multidisciplinary scientists, plastics manufacturers, and end users. The emergence of these materials is not merely a hope, it is a necessity because, as Anne Bergeret puts it: “In all our studies, we see the need for an integrated, interdisciplinary approach, combining the skills of materials specialists like us with those of farmers, biologists and chemists, for a comprehensive understanding and the optimal use of biomass.”
Read more on the blog What is a composite material?
Find out more about the research in agro-based composites at Mines Douai
Find out more about the use of biomass for materials
[box type=”shadow” align=”” class=”” width=””]
Reminder: What is a composite material?
Just like wattle and daub, made of straw and mud, a composite material is created from a fiber reinforcement and a binder called the matrix. Glass and carbon fibers are currently the most commonly used fibers, but they are facing competition from plant fibers, which facilitate recycling and decrease the material’s environmental impact.
The composite’s matrix is generally a thermoplastic or thermosetting polymer. When it is thermoplastic, the polymer is heated to be liquefied and combined with fibers, then cooled to form the final solid material. A thermosetting polymer is originally liquid and easily incorporates the fibrous reinforcements, but it must then be heated in order to harden and form the final composite material. Polymer matrices are also called organic matrices, but they are not the only matrices that exist. There are also ceramic and metal matrices.
Through the careful combination of fibers and the matrix, composite materials offer unusual mechanical properties, which few other materials can offer. The specifications, which dictate the final target properties based on the future use of the part, are what generally define the choice of fibers (type, content, orientation, cut/continuous/woven/braided, etc.) and of the matrix.[/box]
Leave a Reply
Want to join the discussion?Feel free to contribute!