Matériaux composites : la course pour aller toujours plus vite
Dans le monde des matériaux, les composites connaissent aujourd’hui un bouleversement aussi important que l’essor des plastiques dans les années 1960. Pour les intégrer massivement dans les marchés à fort volume de production — automobile, aéronautique, ferroviaire, etc. — il est nécessaire de réduire encore les temps de mise en forme des pièces. Un objectif complexe, atteignable en repensant la composition et l’architecture des matériaux, en adaptant les procédés de fabrication utilisés, et en s’appuyant sur les nouveaux outils de simulation numérique.
« Il y a quinze ans, nous étions contents lorsque nous pouvions sortir une pièce complexe en composites structuraux en cinq minutes » se rappelle Patricia Krawczak, chercheuse en matériaux à IMT Lille Douai. En 2017, les exigences industrielles sont plus strictes. Les propriétés mécaniques des composites intéressent de nombreux secteurs, dont les transports. Plus résistants, plus légers, disposant d’une durée de vie plus longue : ces nouveaux matériaux ouvrent la porte à des produits de rupture, et offrent de nouvelles perspectives économiques. Il faut donc pouvoir les intégrer massivement dans les marchés à fort volume de production, comme l’automobile. L’Alliance pour l’industrie du futur considère ainsi la diminution des temps de cycle de mise en forme et de fabrication, ainsi que le développement de procédés « hautes cadences » comme des grands enjeux industriels actuels auxquels sont confrontés les composites. Pour les pièces automobiles, l’objectif est fixé à des durées de l’ordre de la minute.
À lire sur I’MTech : Quèsaco un matériau composite ?
Sollicités par les industriels pour répondre à ce défi, les scientifiques travaillent à atteindre cette cible. Afin d’y parvenir, les résines plastiques utilisées comme matrice pour imprégner les renforts fibreux ont depuis quelques temps déjà été modifiées. De résines thermodurcissables — se solidifiant lorsqu’elles sont chauffées — les chercheurs sont passés à des résines thermoplastiques — elles fondent avec la chaleur et se solidifient lorsque la pièce revient à température ambiante. « Les temps de cuisson des thermodurcissables sont assez longs, même si les fournisseurs de ce type de matrice progressent et s’efforcent de les réduire » explique Patricia Krawczak. En revanche, les thermoplastiques peuvent être mis en forme rapidement par exemple par un procédé de compression à chaud, l’estampage, ou encore par une technologie d’injection sur préforme fibreuse, sans nécessiter de cuisson ultérieure. « En ce sens, ces résines sont favorables à une réduction du temps de cycle » poursuit la chercheuse.
Une approche globale « matériaux/procédés/produits »
Cependant, il ne suffit pas seulement de modifier la nature de la résine pour diminuer le temps de mise en forme. Sur les pièces visant de hautes performances mécaniques, il est primordial d’éviter les défauts tels que les bulles d’air enclavées dans le matériau. Il convient donc de s’assurer que la résine thermoplastique, une fois rendue liquide par élévation de température, pénètre bien entre toutes les fibres du renfort. Or ces résines-là sont connues pour être plus visqueuses que les résines thermodurcissables. Pour être compétitif et profiter de la capacité de mise en forme rapide des thermoplastiques, il faut alors réduire la viscosité des résines. « Nous travaillons avec des chimistes pour mettre au point des polymères qui gardent les mêmes propriétés d’usage une fois solidifiés, tout en étant plus fluides à la température de mise en œuvre » pointe Patricia Krawczak.
Les chercheurs en matériaux peuvent également jouer sur l’architecture des renforts. Au sein du composite, les fibres se présentent sous forme de mèches constituées de filaments. Elles peuvent être assemblées – tissées, tressées ou cousues – de différentes manières. « La façon dont est constitué le renfort influence les propriétés du matériau composite final, mais aussi la perméabilité de la préforme fibreuse, et de ce fait l’écoulement de la résine au sein du renfort » souligne Patricia Krawczak. Afin de trouver la bonne structure avec un équilibre entre propriétés mécaniques et perméabilité adéquat, l’équipe de la chercheuse collabore également avec des concepteurs de renforts fibreux.
Un autre levier d’action est enfin le procédé de fabrication lui-même, et notamment son adaptation aux spécificités des matériaux qui constituent le composite lui-même : la matrice polymère et la fibre de renforcement. « Notre équipe a développé des procédés hybrides rapides intégrant plusieurs étapes en une seule opération de moulage, en couplant par exemple injection sur renfort et compression ou encore thermoformage et surmoulage » précise Patricia Krawczak. Outre des temps de cycle de fabrication réduits, cette hybridation de procédés permet une diminution significative du nombre de composants élémentaires à assembler pour produire une pièce complexe. Un bénéfice appréciable pour les équipementiers plasturgistes partenaires d’IMT Lille Douai.
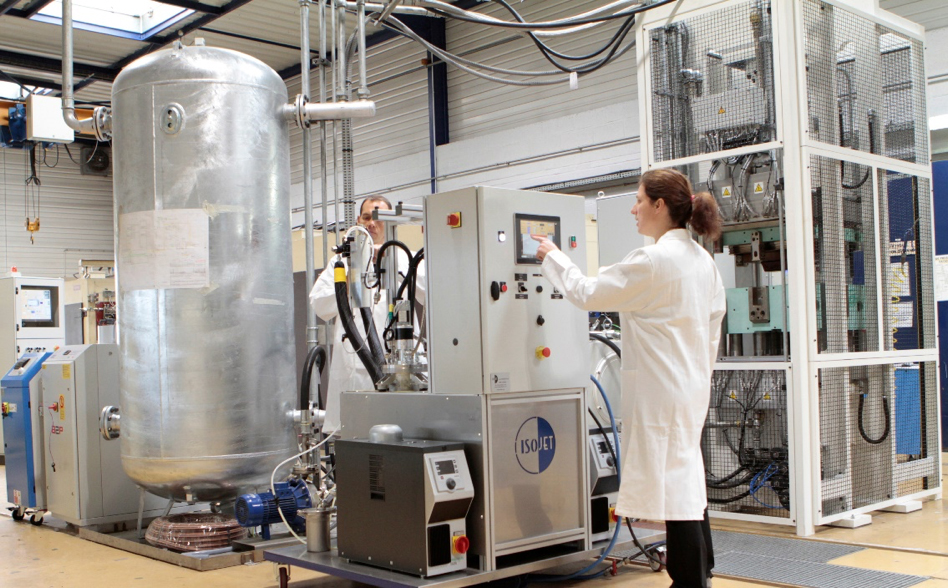
Plateforme d’optimisation de nouveaux procédés composites (POPCOM). Photo : IMT Lille Douai.
Le numérique pour identifier les couples matériaux-procédés optimaux
En pratique, les matériaux composites autorisent une multiplicité impressionnante de combinaisons ‘’matrice polymère / renfort fibreux / procédé de mise en forme’’, encore accrue par les récentes innovations des producteurs – chimistes et tisseurs – et des transformateurs. Pour accélérer la conception des pièces industrielles, les chercheurs développent des chaines d’ingénierie virtuelle. En s’appuyant sur une plateforme technologique équipée d’outillages prototypes et de démonstrateurs représentatifs des procédés de fabrication industriels, ils analysent, identifient, et modélisent les mécanismes d’imprégnation. Ils complètent et améliorent ainsi les outils numériques de simulation de mise en forme.
« Par exemple, nous avons travaillé il y a quelques années avec une résine fortement réactive ayant un temps de gel de l’ordre d’une minute » illustre Patricia Krawczak. « Mais les logiciels de simulation disponibles ne prenaient pas en compte à l’époque la variation spatiale et temporelle de la viscosité de telles résines polymérisant très rapidement. Il a donc fallu mettre à jour l’outil numérique en lui intégrant un modèle spécifique couplant thermocinétique réactionnelle et écoulement ». Cela a permis par la suite de simuler avec pertinence l’imprégnation de différents types de renforts avec cette résine sur des géométries de pièces de carrosserie automobile relativement complexes. En procédant à des tests numériques, le nombre de combinaisons explorées est bien plus élevé. Les chercheurs peuvent alors progresser plus vite, et identifier les meilleures configurations pour optimiser les technologies de fabrication. Ils parviennent ainsi à réduire les temps de cycle tout en maintenant qualité et performances d’usage.
En étudiant virtuellement les matériaux, mais également les procédés utilisés, les scientifiques peuvent même oser des méthodes contre-intuitives. Ce fut le cas lors d’un projet européen alliant IMT Lille Douai à des industriels pour la réduction du temps de cycle de moulage d’un plancher automobile. « En prenant en compte dans nos modèles la déformation des tissus de fibres lors du drapage et ses conséquences sur l’écoulement local de la résine, nous avions alors simulé un procédé. Nous avions proposé des points d’injection séquentielle de résine, des canaux de distribution et des évents à des endroits de la pièce qui n’étaient a priori pas les plus logiques pour les industriels » se remémore Patricia Krawczak. Mais le modèle numérique avait pourtant bien prédit une imprégnation plus rapide et plus homogène du renfort par la résine avec une telle stratégie. Un résultat confirmé ensuite par les validations expérimentales réalisées à échelle réelle.
Aujourd’hui, les chercheurs poursuivent cette démarche scientifique appuyée par des collaborations industrielles pour explorer le potentiel de nouveaux matériaux et de procédés innovants. Les outils numériques évoluent pour simuler avec pertinence de nouvelles variantes technologiques et accompagner l’essor des fibres naturelles dans les composites. Poreuses, celles-ci absorbent une partie de la résine et gonflent. Il faut donc prendre en compte ce phénomène dans les simulations, en espérant que cela débloque de nouveaux scénarios plus performants. Les temps de cycle ne s’améliorent plus à coup de plusieurs minutes comme il y a une quinzaine d’années, mais plutôt de dizaines de secondes. Pour des industries qui produisent potentiellement plusieurs milliers de pièces composites par jour, le gain n’en reste pas moins considérable.
Trackbacks (rétroliens) & Pingbacks
[…] Matériaux composites : la course pour aller toujours plus vite […]
[…] Matériaux composites : la course pour aller toujours plus vite […]
Laisser un commentaire
Rejoindre la discussion?N’hésitez pas à contribuer !